Bugatti ide korak dalje od konkurencije i probija potpuno novi teren u proizvodji auto delova
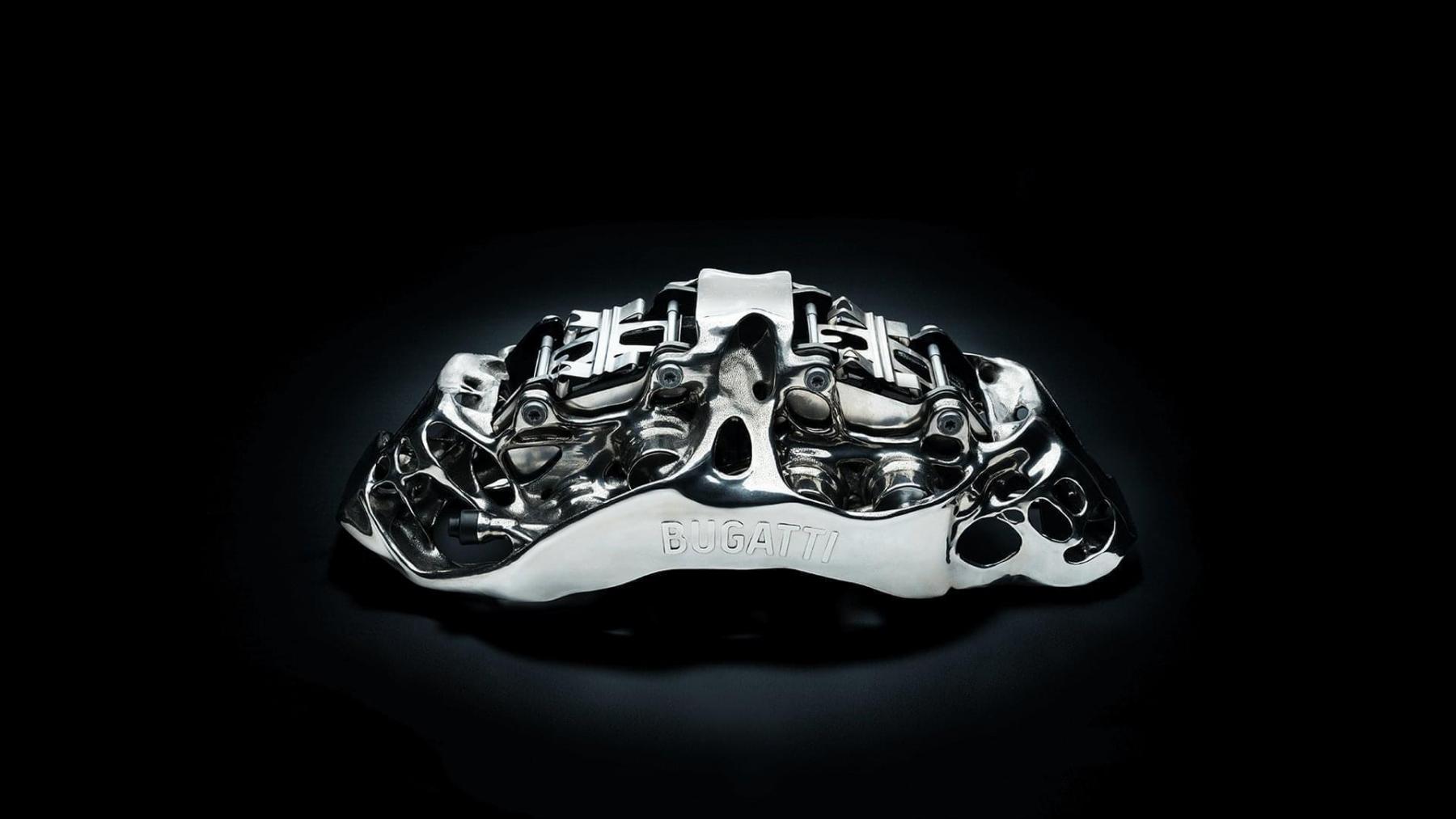
Bugatti-jev najnoviji model, Chiron, trenutno ima najveće i najjače kočnice, kao i kočione čeljusti u auto industriji. Nije lako zaustaviti najbrži automobil na svetu. Bugatti-jevi inžinjeri, razvijali su nove kočione čeljusti od nule, a ideju, inspiraciju, kao i način rada kočnica dobili su iz moto sporta. Novi dizajn kočionih čeljusti kombinuje minimalnu težinu sa maksimalnom čvrstoćom.
Sa novorazvijenim 3D štampanim kočionim čeljustima, Bugatti ide korak dalje od konkurencija i probija potpuno novi teren u proizvodji auto delova.
Bugatti koristi posebnu titanijumsku leguru, koja je najviše zastupljena u avio industriji i koja ima znatno bolje mehaničke i fizičke osobine od aluminijuma. Ova legura koristi se za izradu komponenti koje trpe visoko opterećenje, kao što su nosači krila, delovi trupa letelice, čak i određeni delovi avionskih motora.
TESTIRANJE KOČIONIH ČELJUSTI. 400KM/H ; 1200C
Kao 3D odšampana komponenta, ova legura ima zateznu čvrstoću od 1.250 N / mm2. To znači da se sila od nešto više od 125 kg može naneti na kvadratni milimetar ove legure titanijuma bez da se materijal probije.
Nova titanijumska kočiona čeljust dugačka je 41 cm, široka 21 cm i visoka 13.6 cm i teži samo 2.9 kg. U poređenju sa aluminijumskom kočionom čeljusti koja je trenutno u upotrebi i teži 4.9kg, Bugatti bi mogao smanjiti težinu kočione čeljusti za oko 40%, a istovremeno osigura još veću čvrstoću.
Do danas, zbog izuzetno visoke čvrstoće legure titanijuma, proizvodnja ovakvih auto delova nija bila izvodljiva, jer je izuzetno teško ili čak nemoguće proizvesti sličan deo na cnc-u ili ga kovati iz komada titanijumskog bloka kao što je to uobičajeno sa aluminijumom.
Uz pomoć tehnologije 3D štampe i 3D štampača izuzetno visokih performansi, izrada ovakvih komleksnih delova je konačno moguća. Takođe, otvaraju se vrata i mogućnosti za izradu još složenijih elemenata i delova, znatno veće čvrstoće i otpornosti od bilo kog dela proizvedenog konvencionalnim proizvodnim procesom.
Više detalja kao i video testiranja i proizvodnje ovog dela možete pogledati ispod :